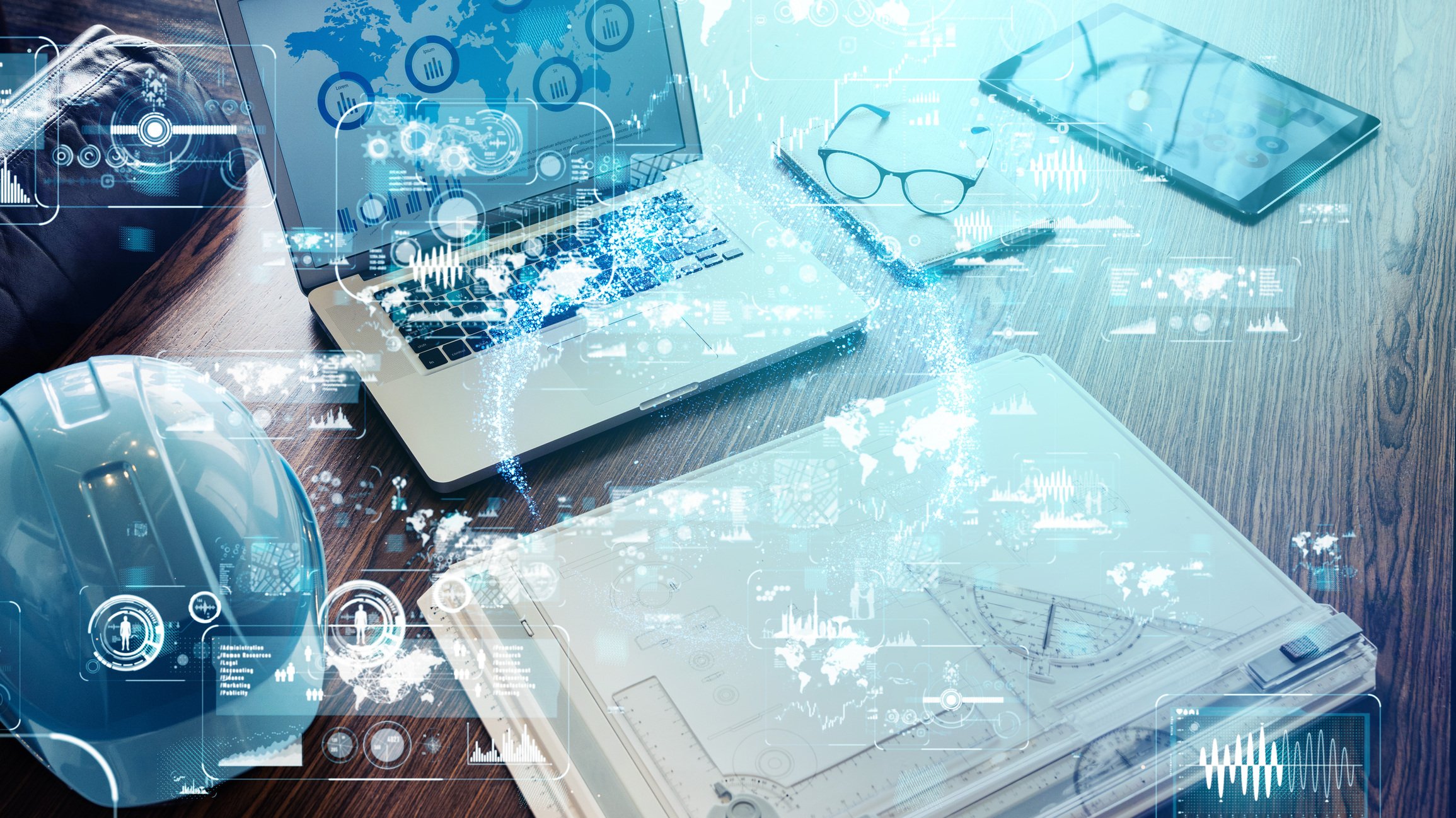
Harnessing Data Analytics to Revolutionize Construction Efficiency and Decision Making
The Benefits of Data Driven Construction
The Benefits of Data Driven Construction
Listen to this post:
In construction, every decision impacts the bottom line, from project timelines to resource management. Using data effectively isn’t just an advantage—it’s essential. Instead of relying on guesswork, real-time data and historical trends can guide your decisions, helping to anticipate challenges, optimize workflows, and improve overall project efficiency. Here’s how data-driven construction is transforming the industry and why adopting these strategies will keep projects on time, on budget, and ahead of the competition.
1. Smarter Decision-Making with Data
Data removes the uncertainty from decision-making. Instead of relying on instinct, tracking real-time project metrics and analyzing past performance can uncover patterns and risks before they escalate. Reviewing historical data helps allocate resources more effectively, and real-time insights ensure that project plans are based on facts rather than assumptions. This approach leads to better planning, fewer delays, and stronger project outcomes.
2. Boosting Efficiency and Productivity
Analyzing workflows, equipment usage, and scheduling helps to eliminate bottlenecks that slow projects down. Tracking productivity trends can highlight where delays occur and pinpoint ways to optimize operations. For example, monitoring equipment usage ensures that assets aren’t sitting idle, while predictive scheduling prevents conflicts that could cause delays. By integrating data into daily operations, teams work more efficiently, and projects move forward with fewer disruptions.
3. Cutting Costs and Maximizing Budgets
Data analytics can identify inefficiencies that drive up costs. Instead of overordering materials or misallocating labor, predictive analytics helps to forecast demand with greater accuracy. Tracking expenses in real time also allows for immediate adjustments before budget overruns occur. Identifying cost-saving opportunities—such as reducing material waste or optimizing procurement—keeps projects financially sustainable and competitive.
4. Enhancing Safety and Reducing Risks
A proactive approach to safety is critical in construction. Using data, potential hazards can be identified before they lead to incidents. Wearable technology and IoT sensors can monitor worker fatigue, detect unsafe practices, and provide real-time alerts to prevent accidents. Analyzing past safety reports and near-misses also helps refine training programs and improve job site protocols, creating a safer work environment for everyone.
5. Preventing Equipment Failures with Predictive Maintenance
Unexpected equipment breakdowns can derail a project. Instead of waiting for machinery to fail, data-driven maintenance helps track performance and detect warning signs before issues arise. Sensors monitoring equipment conditions—such as vibration levels or temperature fluctuations—can predict failures in advance, allowing maintenance to be scheduled at the right time. This reduces costly downtime and extends the lifespan of essential tools and machinery.
6. Building More Sustainably
Sustainability in construction isn’t just about compliance—it’s about efficiency. Tracking energy consumption, material use, and waste production helps identify ways to reduce environmental impact while improving cost-effectiveness. Optimizing logistics to lower fuel consumption, selecting sustainable materials, and monitoring carbon footprints all contribute to greener building practices. Additionally, using data to ensure compliance with environmental standards can help secure green building certifications.
7. Improving Collaboration and Communication
Miscommunication can lead to costly errors and delays. Using centralized data platforms ensures that all stakeholders—architects, engineers, contractors, and clients—are working from the same information in real time. Cloud-based project management tools reduce misunderstandings, streamline approvals, and improve coordination across teams, keeping projects running smoothly.
8. Maximizing the Benefits of Building Information Modeling (BIM)
BIM offers a digital representation of a project’s physical and functional characteristics, allowing for better design coordination and construction planning. By integrating multiple data sources, BIM enables teams to simulate building performance, analyze materials, and identify potential conflicts before construction begins. This reduces costly design changes and improves long-term facility management, making projects more efficient from start to finish.
9. Maintaining Quality with Real-Time Monitoring
Tracking critical project conditions—such as temperature, humidity, and structural integrity—ensures that quality standards are met throughout construction. For example, real-time monitoring of concrete curing conditions helps maintain structural strength, preventing defects and costly rework. Immediate feedback allows for quick adjustments, keeping the project on track and minimizing errors.
10. Staying Competitive and Driving Innovation
Construction firms that embrace data-driven strategies are better positioned to compete in an evolving industry. Access to real-time insights allows for faster decision-making, improved efficiency, and greater adaptability to market changes. Using data to refine processes and explore new technologies leads to innovation and smarter ways of working. As the industry continues to evolve, leveraging data will be essential for delivering better projects on time, on budget, and with higher quality.
Conclusion
Data-driven construction is about making smarter choices that lead to better outcomes. By using data to guide decisions, optimize resources, and improve safety, projects can run more efficiently and cost-effectively. Whether it’s predictive maintenance, real-time monitoring, or improving collaboration, integrating data into construction processes ensures that projects are completed with fewer risks and greater success. The future of construction belongs to those who can harness the power of data to build smarter and more effectively.
Subscribe and stay up to date with the newest posts delivered right to your inbox!